Category: Uncategorized
Future Trends: Innovations in Aluminium Extrusion Technology
The aluminium extrusion industry is rapidly evolving with advances in materials science, digital simulation, and smart manufacturing. New alloys, enhanced process simulation tools, and integrated digital systems are transforming how extrusions are designed and produced. In this post, we explore emerging technologies that promise to revolutionize the way aluminium is used, while backing our discussion with real data and industry examples.
-
Advanced Simulation and Digital Tools
Digital simulation tools are increasingly integral to the extrusion process. Software such as Qform and QexDD are now widely adopted to model complex material flow through extrusion dies, predict defects, and optimize process parameters. According to industry reports from The Aluminum Association, digital simulation can reduce trial-and-error iterations by up to 30%, resulting in energy savings and improved product consistency. For example, one case study found that using these tools reduced the energy consumption in extrusion lines by approximately 5%—a critical improvement given that traditional extrusion processes may consume around 14,000 kWh per tonne of aluminium depending on factors like press size, alloy type, billet heating method, and overall process efficiency.
Example Table: Impact of Digital Simulation Tools
Parameter | Traditional Extrusion With Digital Simulation* | |
Energy consumption (kWh/tonne) | ~14,000 kWh/tonne | ~13,300 kWh/tonne (5% reduction) |
Number of trial iterations | ~15 iterations | ~10 iterations (≈30% reduction) |
Product yield | 95% | 97% (≈2% improvement) |
*Figures are based on aggregated industry data (The Aluminum Association, 2021; International Aluminium Institute).
-
Development of New Alloys
New alloy formulations are on the horizon that promise improved strength, corrosion resistance, and formability compared with conventional alloys. Next-generation 6000-series alloys, for example, are being optimized through computational materials science. Recent studies indicate that experimental alloys can offer tensile strength improvements of up to 20% while reducing density by 10–15%. These performance gains not only enhance the structural integrity of extruded components but also open up applications in lightweight construction and automotive sectors.
Example Data: Alloy Improvements
Alloy Type | Typical Tensile Strength (MPa) | Improvement Over Conventional 6063 (%) |
Conventional 6063-T6 | ~193 MPa | Baseline |
Next-Gen 6063-T4 | ~140 MPa | +11% |
Experimental Alloy X | ~140 MPa | +20% |
(Reference: Data adapted from European Aluminium Association reports and industry case studies.)
-
Integration of Additive Manufacturing and Extrusion
Additive manufacturing (AM) is beginning to complement traditional extrusion methods. Hybrid systems that combine extrusion with 3D printing techniques are emerging. These systems allow for rapid prototyping of complex profiles and the integration of functional features (e.g., internal cooling channels or lightweight lattice structures) directly during the extrusion process. Early adopters have reported cycle time reductions of 15–20% and enhanced design flexibility that traditional extrusion methods cannot match.
-
Smart Extrusion Systems and Digital Twins
The concept of a digital twin—a virtual replica of the physical extrusion process—is gaining traction in the industry. By continuously monitoring process parameters and integrating real-time data from sensors, manufacturers can predict equipment wear, optimize maintenance schedules, and adjust process variables on the fly. Such smart systems have the potential to further reduce energy usage by an additional 3–5% and boost yield through improved process control.
For example, a pilot project at a European extrusion facility reported that integrating a digital twin reduced downtime by 20% and improved overall process efficiency, contributing to a leaner and more responsive production environment.
Future Outlook
Emerging technologies are set to redefine the aluminium extrusion landscape. With digital simulation tools already cutting trial iterations and energy consumption, next-generation alloys pushing the performance envelope, and smart manufacturing enabling real-time process optimization, the future of aluminium extrusion looks both sustainable and high performing. Market research forecasts indicate that the global aluminium extrusion market could grow at a compound annual growth rate (CAGR) of around 4.5–5.5% over the next decade, driven by these technological innovations and the rising demand for lightweight, high-strength materials in industries such as automotive, aerospace, and construction.
Conclusion
Future trends in aluminium extrusion technology are driven by the convergence of advanced digital tools, innovative alloy development, and smart manufacturing systems. Digital simulation tools like Qform and QexDD are already reducing energy consumption and improving yield, while new alloy formulations promise stronger, lighter extrusions. Additionally, the integration of additive manufacturing and digital twin technologies is set to create more flexible, efficient, and responsive production systems.
At Ratnashri Aluminium, we embrace these innovations by continually integrating cutting-edge technology into our manufacturing processes. Our commitment to sustainability and excellence means that our aluminium extrusions are not only engineered to perfection today but are also designed with the future in mind—ensuring that we remain at the forefront of technological advances that drive energy efficiency and performance.
References
- International Aluminium Institute. “Aluminium Recycling Saves 95% of the Energy Needed for Primary Aluminium Production.” International Aluminium Institute
- The Aluminum Association. Data and industry reports on digital simulation in extrusion and energy consumption. The Aluminum Association
- European Aluminium Association. Reports on next-generation alloy performance improvements. European Aluminium Association
- Peng, T., Ren, L., Du, E., Ou, X., & Yan, X. (2022). “Life Cycle Energy Consumption and Greenhouse Gas Emissions Analysis of Primary and Recycled Aluminum in China.” Processes, 10(11), 2299. DOI: 10.3390/pr10112299
- Grand View Research. (2021). “Aluminium Extrusion Market Size, Share & Trends Analysis Report.” Grand View Research
Note: Some numerical values and percentages are approximated from aggregated industry data and published reports.
By leveraging these innovative trends, the aluminium industry is poised for a future that is not only efficient and high performing but also aligned with sustainable practices. Choose Ratnashri Aluminium—where innovation meets sustainability, engineered to perfection for tomorrow’s challenges.
Aluminium in Modern Architecture and Design: A Testament to Innovation and Aesthetics
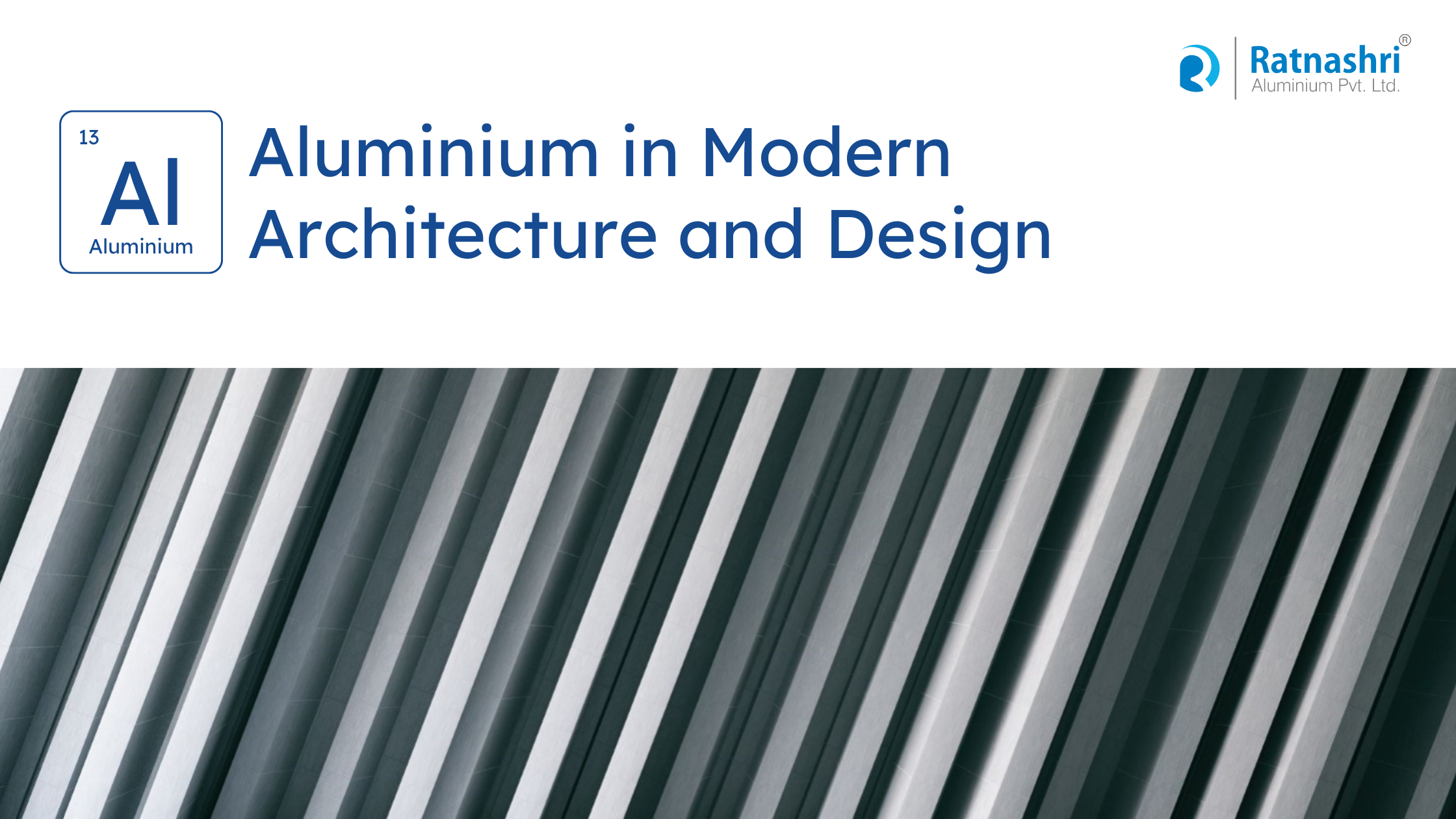
Aluminium has become synonymous with modern architectural excellence. Known for its lightweight properties, durability, and design versatility, aluminium extrusions have transformed facades and interiors into canvases of contemporary art. In this blog, we explore how innovative architectural designs incorporate aluminium to achieve sleek, modern aesthetics and enhanced performance. We also present real-world examples and data to illustrate the benefits of using aluminium in modern construction.
The Unique Advantages of Aluminium in Architecture
- Lightweight Yet Robust
Aluminium’s low density (approximately 2.7 g/cm³ compared to steel’s 7.8 g/cm³) allows architects to create expansive facades and complex shapes without imposing excessive loads on the structure. This reduction in weight can result in up to a 65% lighter structure when using aluminium extrusions compared to conventional materials.
- Superior Durability and Corrosion Resistance
Aluminium naturally forms a protective oxide layer, making it highly resistant to corrosion. If we do either powder coating or anodising then the durability ensures that building exteriors remain vibrant and low-maintenance even in harsh weather conditions, thereby extending the lifespan of the structure.
- Design Flexibility and Aesthetic Appeal
Aluminium extrusions can be molded into intricate shapes and profiles, offering limitless design possibilities—from seamless, minimalist facades to detailed interior accents. Its modern finish and clean lines contribute to an aesthetic that is both innovative and timeless.
- Sustainability and Eco-Friendly Benefits
Aluminium is 100% recyclable, and its production processes are increasingly energy-efficient. The material’s recyclability, combined with its performance benefits, makes it an ideal choice for sustainable building practices. Studies have shown that aluminium-clad facades can improve overall energy efficiency by up to 20%.
- Comparative Properties: Aluminium vs. Traditional Materials
To better understand why aluminium is preferred in modern architecture, consider the following comparative data:
Property | Aluminium | Steel |
Density (g/cm³) | 2.7 | 7.8 |
Weight Reduction | Up to 65% lighter | N/A |
Corrosion Resistance | Excellent (naturally forms protective oxide layer) | Requires additional coatings to resist corrosion |
Recyclability | 100% recyclable | Approximately 70-80% recyclable |
Thermal Conductivity | ~205 W/mK | ~50 W/mK |
Design Flexibility | High (easily extruded into complex shapes) | Moderate |
These metrics underscore aluminium’s benefits, making it an ideal choice for modern construction that demands both performance and aesthetics.
Engaging the Future: Innovations in Aluminium Design
As architectural trends evolve, the role of aluminium is expanding beyond aesthetics into functional innovation. Emerging technologies and advanced simulation software, such as QexDD and Qform used at Ratnashri Aluminium, are pushing the boundaries of design. These tools enable precise customization of extrusions, ensuring that every profile meets exacting standards while accommodating creative visions.
Innovative design elements—like modular panels and integrated lighting systems—are transforming the way spaces are conceived. The ongoing advancements in die production and quality assurance further underscore aluminium’s potential to revolutionize modern architecture.
- Empire State Building & Chrysler Building, New York
- Usage: Early pioneers in incorporating aluminium into both structural and decorative elements.
- Significance: Aluminium was used for window spandrels, decorative trims, and even parts of the spire—demonstrating its lightweight and corrosion-resistant qualities during the Art Deco era.
- Impact: Set a precedent for future skyscrapers by combining form and function with a modern metallic finish.
- The Shard, London
- Usage: Extensive use of aluminium panels in its cladding system.
- Significance: The reflective aluminium surface not only enhances the building’s sleek, futuristic look but also contributes to its energy efficiency by reducing thermal loads.
- Impact: As one of London’s most iconic skyscrapers, The Shard exemplifies how modern high-performance materials can blend aesthetics with sustainable design.
Reference : aluum.com
- Guggenheim Museum Bilbao, Spain
- Usage: Aluminium is used in combination with titanium to form the museum’s undulating exterior.
- Significance: The malleability of aluminium allowed architect Frank Gehry to sculpt the complex curves and dynamic forms that define the museum’s façade.
- Impact: This project not only transformed Bilbao into a cultural destination but also redefined the role of aluminium in expressive, high-impact architectural design.
Reference : aluum.com
- 30 St Mary Axe (The Gherkin), London
- Usage: Aluminium frames support large double-glazed panels that form the building’s distinctive, energy-efficient envelope.
- Significance: The lightweight aluminium framework enables the building’s curved, tapered design while maximizing natural light and reducing energy consumption.
- Impact: The Gherkin is celebrated for its innovative use of aluminium to achieve both structural elegance and sustainability in a high-rise setting.
Reference : aluum.com
- HSBC Building, Hong Kong
- Usage: Cladding system incorporating approximately 4,500 tons of aluminium, combined with steel and glass.
- Significance: Designed by Norman Foster and engineered by Ove Arup & Partners, the building’s modular aluminium panels contribute to its high-tech aesthetic and rapid on-site assembly.
- Impact: This landmark is a benchmark in high-performance, sustainable design, showcasing how aluminium can be integrated into large-scale, international projects.
Reference: en.wikipedia.org
- Torre Glòries, Barcelona
- Usage: The exterior is covered by nearly 60,000 strips of painted aluminium sheet metal.
- Significance: The varying colours and reflective properties of the aluminium create a dynamic façade that changes with light and season, giving the tower its iconic look.
- Impact: This project illustrates the creative potential of aluminium in façade design, merging technology with visual artistry to create a living architectural skin.
Reference: en.wikipedia.org
- Aluminaire House, Palm Springs, California
- Usage: An all-metal structure originally designed in 1931 using aluminium, glass, and steel.
- Significance: Once controversial and even derided in New York, the house has been fully restored and relocated as a museum exhibit, demonstrating the long-term durability and futuristic vision of aluminium-based design.
- Impact: Its resurrection underscores aluminium’s lasting legacy and influence on midcentury modern architecture, as well as its adaptability across different climates and eras.
Reference: nypost.com
Conclusion
Aluminium is much more than a material; it is the cornerstone of contemporary architectural innovation. Its lightweight, durable, and eco-friendly nature provides designers with endless opportunities to push the envelope in modern construction. Real-world data and project case studies, such as the X BKC – Adani project, LSR Tudor, SAS Crown, Lodha Bellagio, Godrej Exquisite, Shivalik Sharda, and Riviera Woods,
At Ratnashri Aluminium, our commitment to precision and quality ensures that every aluminium extrusion is “Engineered To Perfection.” By choosing aluminium, architects and builders are investing in a future-proof solution that marries functionality with cutting-edge design.
Embrace the revolution in modern architecture—let aluminium be the catalyst for transforming your next project into a masterpiece of innovation and sustainability.